Even narrow aisles are no problem for HUBTEX vehicles.
Even in narrow aisles, the HUBTEX reach truck delivers a powerful performance.
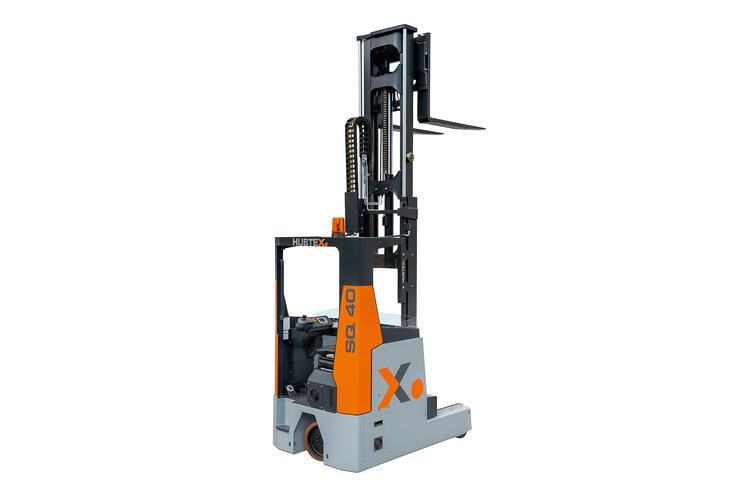
HUBTEX reach trucks can also store heavy loads on racks despite their narrow dimensions.
Whether in mechanical engineering or other branches of industry, sooner or later, process optimisation requires the transport of heavy and complex loads. Carl Schlenk AG, the manufacturer of metal powders, pigments, and foils has its headquarters in Barnsdorf near Roth (Bavaria), Germany. In its rolling mill, semi-finished goods weighing up to 4 t are transported day in day out. These weights present a challenge to conventional fork-lift reach trucks. At the same time, the company faces the difficulty to organise its flow of material in spaces that are sometimes rather narrow. The company has been established for a long time and is located in a historic building. Needless to say, its production hall and warehouse provide only limited space and the storage aisles are narrow. However, in order to move large and heavy metal coils safely and quickly, Schlenk relies on special designs provided by Hubtex. The electric multi-directional sideloader SQ 40 combines compact dimensions with high load capacities and safe handling features.
Schlenk was founded in 1879 and currently employs a staff of 930 worldwide in production locations in Europe, the US, and China. The enterprise is a holding company and divides its business into the two areas of metallic pigments and metal foils. The metallic pigments are used in the paint and plastic industry in order to generate a metallic effect, which is quite common in the automotive finishing industry. The division Schlenk Metallfolien GmbH & Co. KG manufactures the thinnest copper foils, copper-based alloys, nickel, white copper, resistance alloys, and fine silver. The foils are used in many application areas. These include solar modules, heat exchangers, surface finishing, and electrical fuses. The foils are also used in medical engineering, and ribbon cables for the automotive industry.
At the end of the production chain, metal foils might be very thin and light; however, at the beginning, the base material is extremely heavy: Each single roll of the copper and silver primary material weighs approx. 3.5 t. Depending on the customer's order, the rolls move through a variety of processing steps during the production. These steps include milling, cutting, and winding, special degreasing methods and galvanic treatment of the semi-finished products. This is where the fork-lift reach trucks are employed to transport the rolls between the various plants. For instance, the forklift truck transports the rolls to and from various stations that include rolling, annealing, rolling again, greasing and annealing again. The finished metal foils are rolled into coils and transported in-house. Before shipping the metal coils, they are stored in a high-rise shelving system or on system pallets.
Since the firm was established, the company has never changed its location; however, the flow of its material has increased dramatically. As Christian Hoffinger, Technical Manager at Schlenk puts it: "With our increasing presence on international markets, the demand for our production processes has grown". "Although our space is still the same and very limited, we can now transport much heavier and complex loads". The expert in the manufacturing of metal foils uses a total production area of approx. 10,000 m². There are 250 storage places at floor level and 750 rack-based pallet storing positions. In the past, Schlenk used standard fork-lift reach trucks with a load capacity of 2.5 t and standard dimensions to move rolls of primary materials and coils for their intralogistic transport purposes. In order to be able to use the old forklift for transporting purposes, its dead weight was substantially increased. Furthermore, the lift height of the conventional forklift truck was rather low and, therefore, the coils could not be stored in the high-rise racks. This is when the company turned to Hubtex. The manufacturer of custom-designed industrial trucks received the order to manufacture a fork-lift reach truck with the same dimensions as a conventional fork-lift, however, with a load-bearing capacity that exceeds the previous capacity by 1.5 t.
The result of this development is the Electric Reach Truck SQ 40: This vehicle has a higher load centre in combination with an increased load capacity and very compact dimensions. With an overall width of 1,300 mm the SQ 40 has a total length of 2,870 mm and a lift height of 2,500 mm. The load centre of the electric multi-directional sideloader is at 600 mm off the ground and the truck can lift coils of up to 4 t 1.5 m high. "Since its delivery, the forklift has been in use continuously. When compared with the previous fork-lift reach truck, the SQ 40 allows us to store our products more safely in the high-rise racks and it allows us to utilise the limited space much better", explains Hoffinger. "Speed and efficiency in transporting finished materials are of the essence in our production. This forklift meets all requirements". The state-of-the-art and ergonomic design of the SQ 40 provides the driver with an unobstructed view of the transported loads. The vehicle is user-friendly and can be operated with finger movements. The layout of the controls inside the operator's cab is clearly arranged. This reduces the training period of the driver.
One of the requirements of the forklift reach truck made by Hubtex is its electric drive unit. In addition to ecological considerations, Schlenk focused on the sensitive metal foils: Soot from the vehicles combustion engine would settle on the foils and cause their discolouration. The electric motor, however, has additional benefits. By employing state-of-the-art control technology with an energy recovery system, the operating time of the fork-lift was increased with the same battery capacity. Therefore, Schlenk can utilise the vehicle throughout an entire work shift without any problems. Moreover, a roller conveyor makes it fast and easy to replace the battery. Since the fork-lift is only placed out of service for a short period of time during a shift, this saves the company time and money. Generally, the SQ 40 requires little maintenance. For instance, the electronic braking system never requires maintenance. The tyres of the SQ 40 are made of polyurethane elastomer – referred to as Vulkollan®. It is known for its excellent wear and tear resistance and minimum wheel height requirements.
Visually, Schlenk's SQ 40 already resembles the new Hubtex design line: The signature orange colour has now faded into the background and black is now more dominant. With the new colour scheme Hubtex contributes to a safer workplace in the warehouse. "Our lift trucks comply with the customer requirements and assist in the efficient implementation of the clients' production processes. Hubtex fork-lifts meet the high demands with respect to user-friendliness and ensure their safe application during in-house production sequences. The new design focuses on increased safety", explains Tobias Schmoll, Project Manager at Hubtex.
Based on the structurally restricted conditions of the factory and the increasing demand for metal products, Schlenk was presented with the challenge to optimise its production processes. The Electric Reach Truck SQ 40 is a special design that allows Schlenk not only to increase its production output but also use its limited warehouse space more efficiently. "For us, the SQ 40 is a long-term solution", explains Hoffinger.