Depending on the turnover rate, storage capacity and budget, there are various solutions for picking long, heavy and bulky goods. Let our product experts advise you on the right picking solution for your application.
Door picking
aiming at the target with laser light
RWD Schlatter AG has significantly simplified the storage and picking processes for doors, door frames and raw materials. An individually configured HUBTEX MK15 electric multidirectional order picking truck drives semi-automatically to the individual rack compartments.
The efficiency gain is enormous: in the new warehouse of RWD Schlatter AG, a specialist in room and functional doors, only a single employee is required to pick the doors and frames at the Roggwil site. At the previous location, two people were needed for this process because at that time a conventional forklift truck was still used for this step. “To fulfill the orders, the desired doors had to be lifted out of the rack by the pallet, placed in the aisle and lifted off individually,” recalls Matthias Tabak, who works at RWD Schlatter as a group leader in production/logistics.
The company wanted to optimize its internal logistics by building a 295 in high warehouse with 210 pallet spaces, 18298 ft² of storage space on the ground floor and 21527 ft² on the basement level, and spoke in advance with potential suppliers – including Rohrer-Marti AG, which acts as the Swiss importer and service partner of HUBTEX. As early as 2021, ideas and possible solutions for simplified order picking were discussed with Rohrer-Marti and the specialists from HUBTEX. The result was a HUBTEX MK15 electric multidirectional order picking truck that was individually customized for RWD Schlatter and can also take over the storage of wooden pallets weighing up to 3307 Ibs to a maximum lifting height.
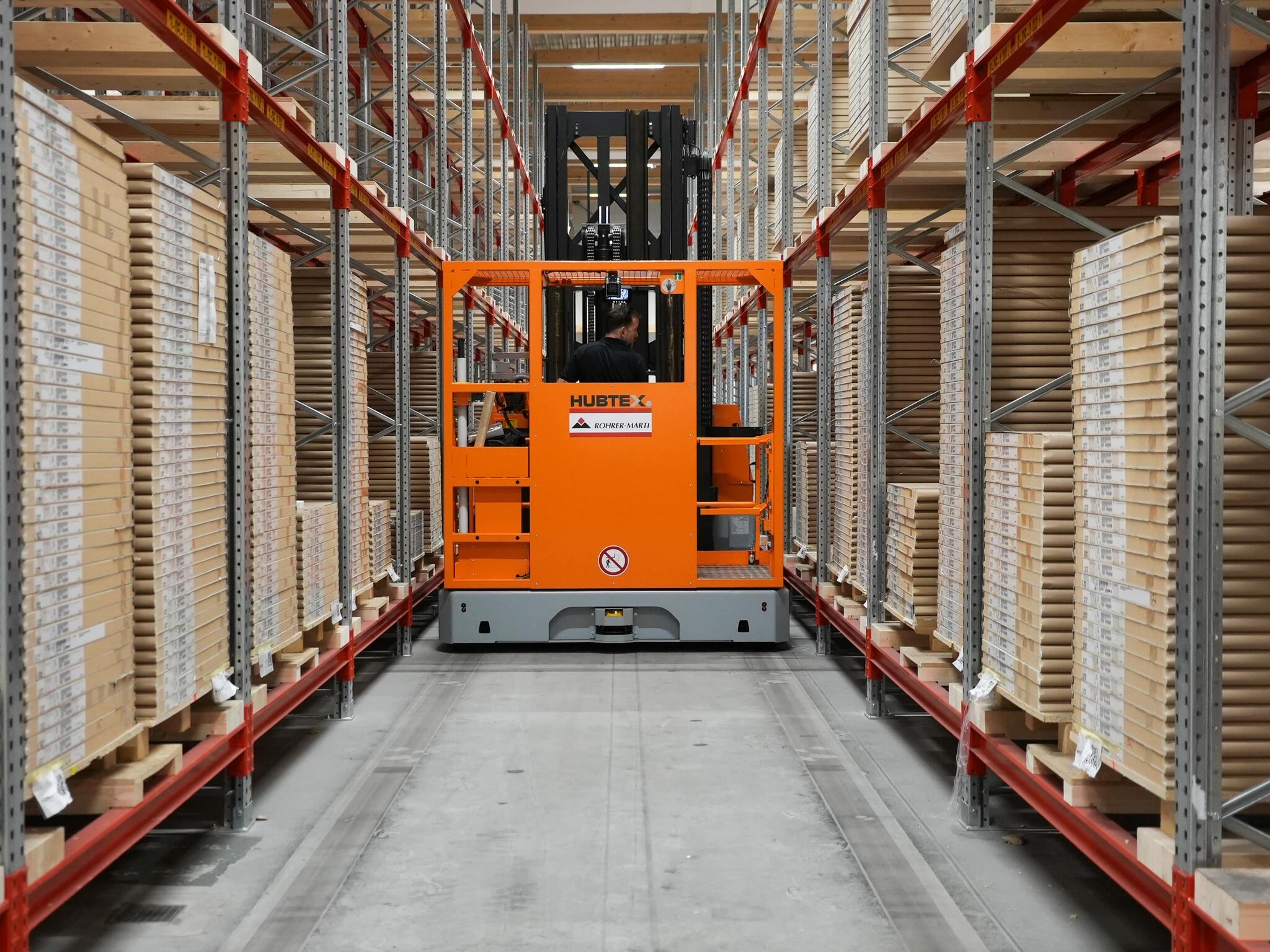
All special requests taken into account
The vehicle was delivered in April 2023 - just one month after completion of the new hall, which has four rows of racking and two aisles.
“The project with HUBTEX went very smoothly and professionally. All of our special requests were taken into account,” confirms Peter Seitz, Head of Project and Process Management. Only seven months passed between the order and delivery of the device. The only thing that was faster was the second forklift truck that RWD Schlatter needed for the new hall in the basement: a HUBTEX Phoenix MQ35 multidirectional sideloader for the raw materials warehouse was available after just six months.
The 153 in long MK15 is controlled by joystick, either from a seated or standing position, and has an order picking platform with an operating stand. The platform enables order picking on both sides and can be raised to a height of 291 in. In front of it, in the direction of travel and view, are the two telescopic forks, which can be extended on both sides and are also height-adjustable together with the load table. This initial lift always allows the picking pallet to be brought into an ergonomically favorable position when processing orders with up to 30 items. The two-part pendulum chassis ensures that all four wheels are in constant contact with the ground thanks to the mechanical level compensation.
Option for the future
The next order item of the current picking order is shown to the operator on a display connected to the company's own warehouse management system in the ERP system via WiFi. To reach the destination, the operator simply has to enter the corresponding rack compartment address on the HUBTEX positioning terminal. The MK15 moves through wire guidance within the only 40 in wide rack aisles. Around 7874 inches of induction wire were laid in the hall floor for this purpose. After the destination address has been entered, the electric multidirectional order picking fork lift truck moves semi-automatically to the shelf compartment. To measure the horizontal position in the aisle, a distance sensor mounted on the lift arm sends a laser beam to a reflector plate mounted at the end of the aisle.
As soon as the horizontal target position is reached, another vertically measuring laser sensor is activated: This measures the current lifting height and detects when the respective storage compartment has been reached with a maximum deviation of 0,79 in. The operator now moves the load table or the picking pallet to the correct height using a joystick, with the help of two cross-line lasers. The required item is then removed from the compartment. In order to make it easier to move the heavy doors, supporting rollers can be inserted on the loading table. As soon as all the doors for an order have been picked up, the picking of the frames that are stored in the neighboring aisle begins.
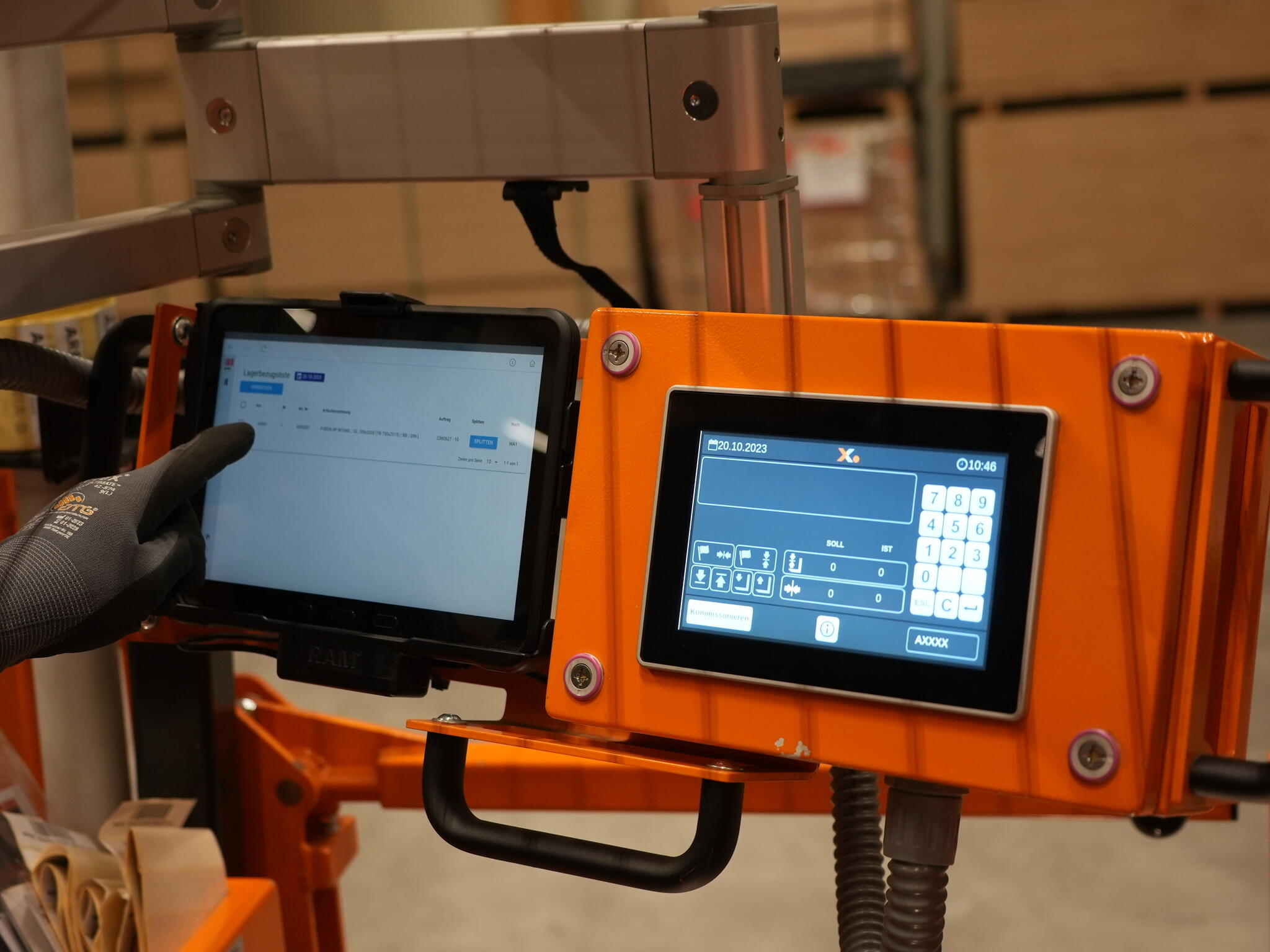
Precise operation
“Working with the MK15 is very precise and easy to understand, which makes it possible to learn the ropes quickly,” reports Antonio Mancuso, who mainly operates the machine and can use it to complete up to 300 picking orders every day.
As soon as the truck is in the lane, the four wheels automatically align themselves for lengthwise drive. With the help of two cameras and a flat screen mounted in the center under the protective roof, the operator can see the route ahead. In addition, a personal protection system integrated into the forklift with laser scanners installed on both sides prevents the MK15 from endangering people or objects in the aisle. When an obstacle is detected, the MK15 is automatically braked. The truck cannot move off again until the person has left the danger area or the object has been removed.
Conclusion:
RWD Schlatter AG has significantly simplified its internal logistics with the individually configured MK15 electric multidirectional order picking truck. The storage and picking processes can be carried out in less time with only half the manpower required for the previous process. This is a major advantage in view of the increasing shortage of skilled workers. In addition, the new hall has a very high storage density because the aisle widths could be reduced to only 4 in.
Discover the benefits for your application
What does RWD Schlatter AG say?
Background: RWD Schlatter AG
RWD Schlatter is a Swiss full-service provider of sustainably manufactured functional doors with safety options such as fire, smoke, sound or burglary protection, as well as interior doors combined with high design standards. With around 200 employees in Switzerland, RWD Schlatter is able to serve the entire value chain from development and production to installation and maintenance.
The company, based in Thurgau, has established a leading position in the Swiss market for building security and is considered a reliable partner for efficient, high-quality complete solutions in construction. With its smartDoors (keyless entry system), digiDoors (which documents, controls and automates the lifecycle of doors) and “service” QR code on every door, RWD Schlatter is also playing a pioneering role in the digitalization of doors. Around 90,000 custom-made wooden doors are produced annually at the headquarters in Roggwil, Thurgau. The history of RWD Schlatter can be traced back to 1884. Since 2007, RWD Schlatter has been part of the Arbonia Group, headquartered in Arbon, Thurgau. Further information can be found at www.rwdschlatter.ch.
Background: Rohrer-Marti AG
Rohrer-Marti AG is one of Switzerland's leading importers of forklift trucks and construction machinery. Since its foundation in 1946, the company has grown steadily and now employs 65 people. The company is present in Zollikofen BE and Echallens Payerne VD and represented throughout Switzerland by regional partners.
The exemplary spare parts service and seamless service organization ensure that all customers can use their forklifts and construction machines without any problems at any time.